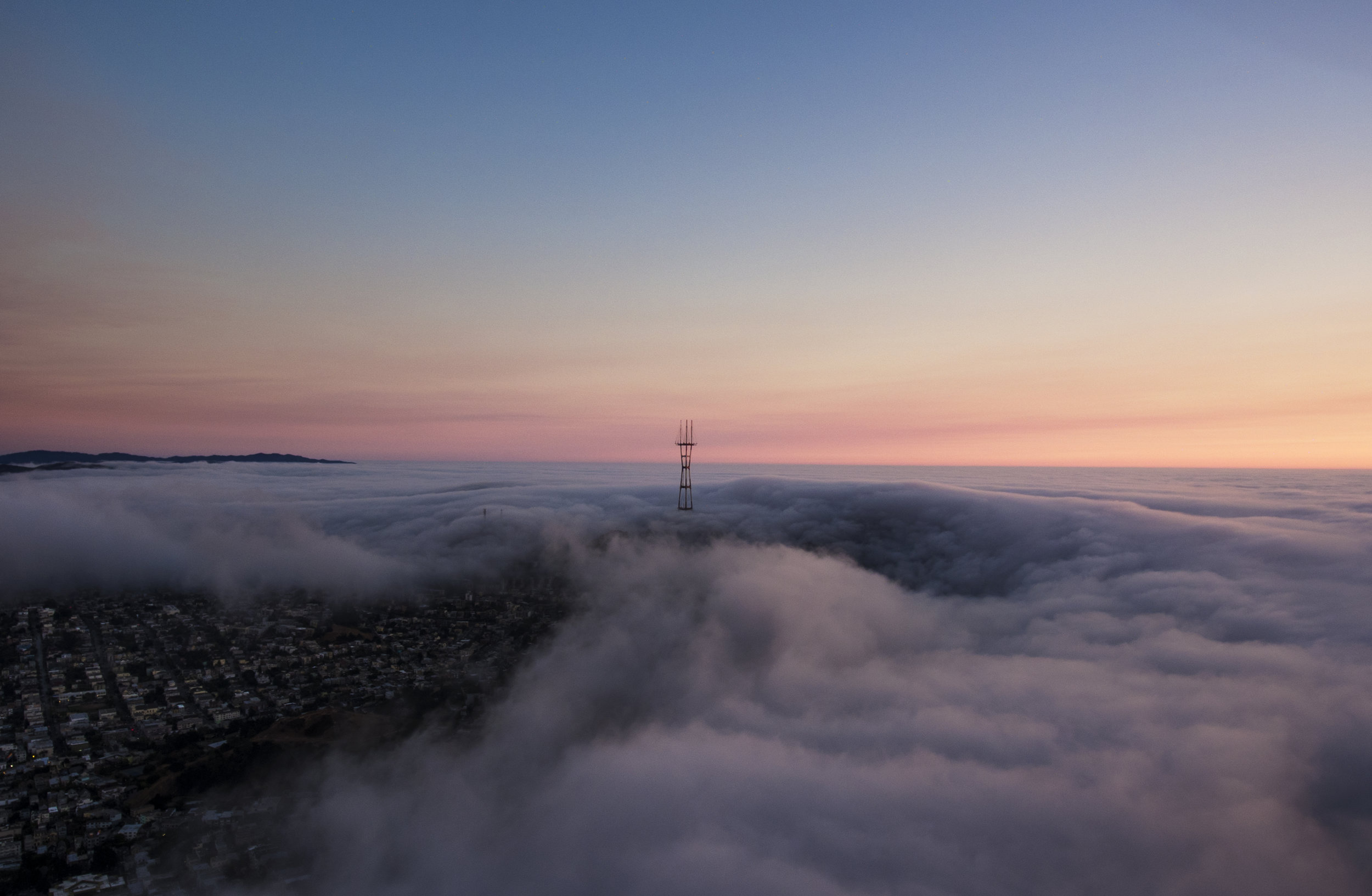
Modernization
As elevators age recurring repairs and shut downs are a sign that your elevator may need a modernization. Aging equipment becomes more difficult to support do to the lack of spare parts availability, difficulty getting electrical schematics and ongoing code changes.
Upgrading your equipment is the best way to significantly improve the safety, reliability and efficiency of your conveyance system(s). Modern systems reduce energy consumption, improve traffic handling capabilities and increases the value of your building or residential property.
Bleyle Elevator has the experience and resources to provide the most appropriate and latest technologies to optimize the results of your modernization.
Bleyle Elevator only uses high quality equipment when performing modernizations. We use only non – proprietary control systems and equipment. This enables any qualified elevator company to maintain your equipment. We believe using non- proprietary equipment is most important factor an owner should consider for long term maintenance expenses. Companies that use their own proprietary equipment require special tools to maintain their equipment. These proprietary tools are generally not available to other elevator companies; this often leaves the building owner with only one service company choice and drives up service and repair costs.
Elevator Preservation Program
A Program Designed To Support & Enhance the Long Term Safety & Operation of Older Elevators
If you have an older elevator and you want to keep it in top operating condition for years to come you must invest in safety and reliability. Through our elevator preservation program we can refurbish your conveyance system(s) so they can perform at their best for decades. This is also a good risk management tool to reduce your conveyance system(s) liability exposure. Older elevators are more prone to safety issues due to their age and they also have fewer safety mechanisms compared to new modern elevators.
Many older elevators, especially ones with original equipment, have had oil and grease service contracts for decades. Often elevator equipment, hoistways, machine rooms, and overhead machine spaces have not been properly cleaned and/or the equipment thoroughly lubricated for an extended period of time. Formal safety equipment testing most likely has not been done since installation. Although thorough safety testing is required by code in most areas of the world this type of testing is not required by code in California. The existing operational capabilities of your conveyances are also most likely unknown. To fully assess the safety & operating capabilities of your conveyance system(s) we suggest the following approach.
Our Preservation Process
Phase I – House Keeping
Bleyle Elevator will complete a comprehensive cleaning of the machine room(s) and related equipment. This includes drive machines, deflector sheaves, motors, controllers, selectors, brakes, overhead machinery rooms, hoistways, hoistway equipment, pits, rails, car tops and all safety equipment. We will also apply new lubricants at all lube points. For hydraulic units, we include filtering the system(s) hydraulic oil, this is to remove contaminants and particulates. No disassembly, repair or adjusting of equipment is included in this phase of work. Housekeeping must be done by a licensed Elevator Mechanic. It allows for a detailed inspection of the elevator components that is beyond the scope of maintenance.
Phase II – Safety & Operational Testing
There most likely has not been any documented safety or operational testing of your drum and/ or traction elevators since they were installed. Most of these conveyance systems are not required by the State Elevator Code to have this type of testing. On conveyance system(s) installed before October 1998 we propose the following testing to be done on each drum and traction elevator.
• Empty and full load testing of motor and elevator for lifting capacity and speed capabilities.
• Megohm testing of the motor winding in both hot and cold conditions will be performed to evaluate the condition of the motor winding.
• At full load and running at leveling speed test the operation of overspeed governor and car safety.
• Perform a functional test of all devices included in safety circuit.
• Evaluate the physical and operational conditions of brake and floor selector and current floor stopping capabilities.
• Functional test of all fire service, seismic operation, telephone operation,emergency lighting and alarm bell systems.
• Submit motor and operational evaluation forms to owner to document existing field conditions. No disassembly, repair or adjustment or equipment is included in this phase of work. Hydraulic elevator testing to be done at time of phase I work.
Phase III – Repair Recommendations and proposals
After completing Phase I & Phase II on each elevator we will submit a list of recommended repairs for the elevator(s). The recommended repairs will be focused on long term safety and reliability.
Phase IV – Complete Owner Approved Repair Proposals
Owner will select and prioritize repair proposals and develop scheduling with Bleyle Elevator. This pro active approach will reduce or eliminate unplanned elevator shut downs and unsafe conditions. Those proposals that support increased safety will receive greater attention in order to reduce liability exposure.
Phase V – Monthly Maintenance
Each elevator will have a monthly one hour Oil & Grease service program. Focus will be on keeping safety equipment and operating devices at their best functional capabilities as well as proper housekeeping and lubrication requirements.